POURQUOI LA CORROSION SE FORME-T-ELLE EN PEINTURE ?
Tout d’abord, il est important de faire la différence entre l’oxydation et la corrosion. L’oxydation est le processus précédant la corrosion, qui est causée par l’attaque de l’oxygène sur un matériau donné. La corrosion, quant à elle, est la conséquence de cette attaque, entraînant une dégradation et une usure du corps du matériau métallique.
Le contact du matériau métallique avec l’oxygène et l’humidité produit un phénomène électrochimique complexe qui est à l’origine de la corrosion. Cependant, en plus de l’humidité, il existe d’autres agents corrosifs tels que :
- les températures élevées ;
- la salinité de l’environnement due à la proximité de la mer ;
- la pollution industrielle.
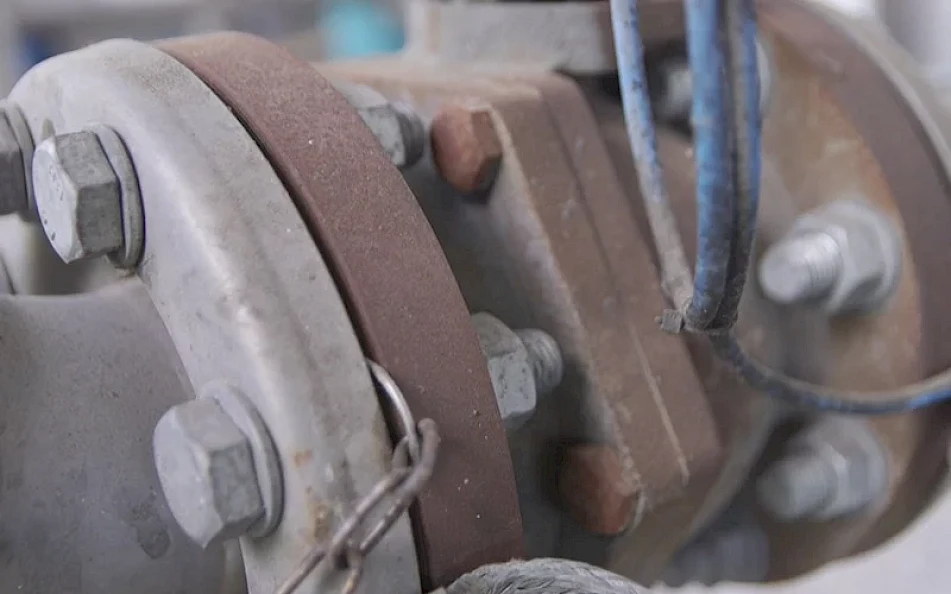
TYPES DE CORROSION DES MÉTAUX
Il existe différents types de corrosion dans la peinture industrielle, qui varient en fonction des conditions environnementales ainsi que des caractéristiques du matériau lui-même.
Corrosion atmosphérique
Il s’agit d’un type de corrosion qui se développe uniformément sur toute la surface du matériau. Elle est principalement due à l’effet des agents corrosifs présents dans l’atmosphère, tels que l’oxygène, le dioxyde de carbone, la vapeur d’eau, les composés de soufre et de chlore.
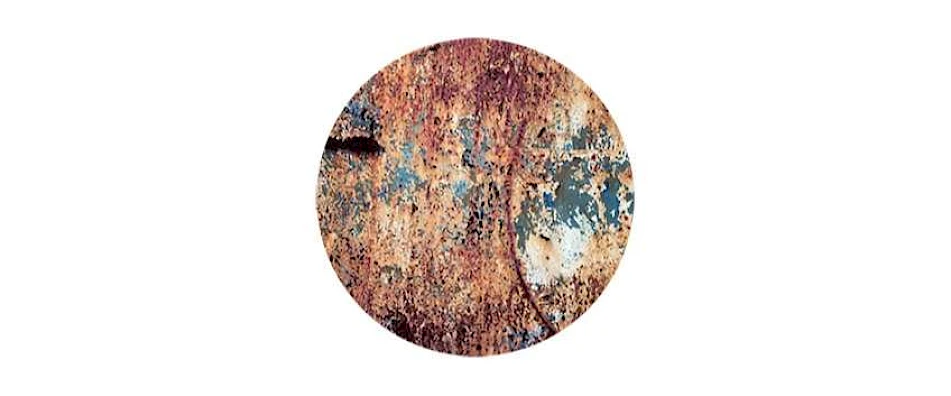
Corrosion galvanique
La corrosion galvanique est un type de corrosion très courant, qui se produit lorsque deux matériaux de potentiel différent sont liés électriquement l’un à l’autre au contact d’un électrolyte, comme l’eau salée. Dans certaines circonstances, la vitesse de réaction de la corrosion galvanique peut être très élevée et il convient donc d’y remédier le plus rapidement possible.
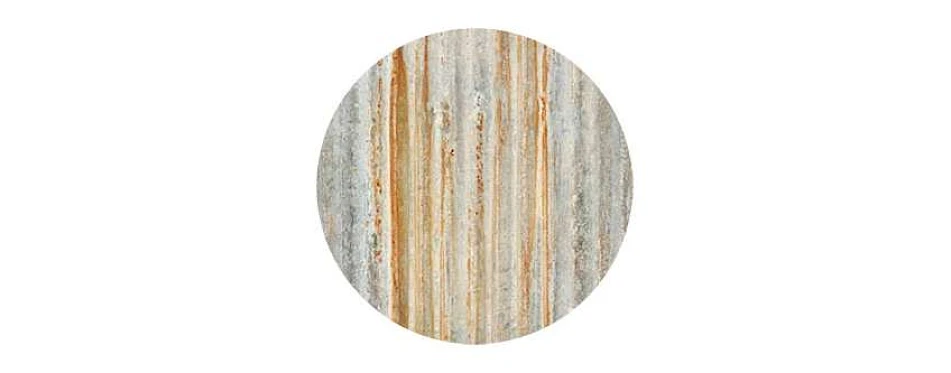
Corrosion par piqûres
La corrosion par piqûres est une attaque généralisée sur toute la surface du métal, accélérée par la présence de chlorures. Il s’agit d’un type de corrosion très dangereux, surtout s’il se produit dans des réservoirs industriels ou des silos contenant des liquides, car il y a un risque de perforation.
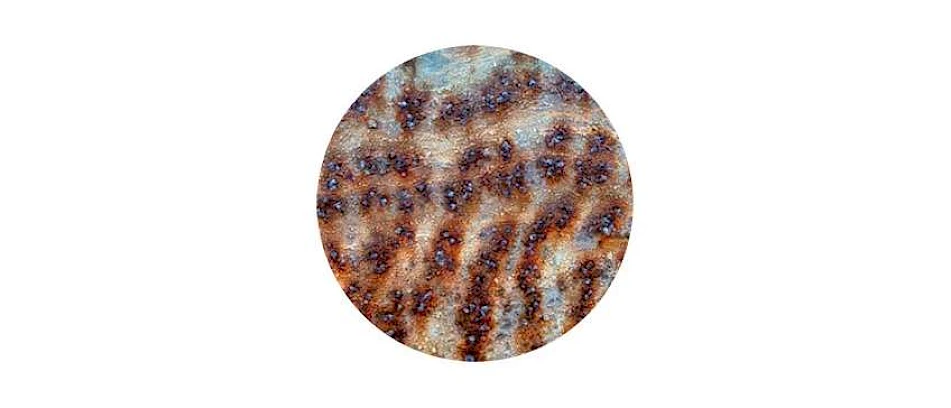
Corrosion par érosion
La corrosion par érosion se produit principalement à l’intérieur de tubes ou de tuyaux, en raison de l’écoulement de liquides qui élimine successivement les couches d’oxyde qui se forment progressivement à la surface.
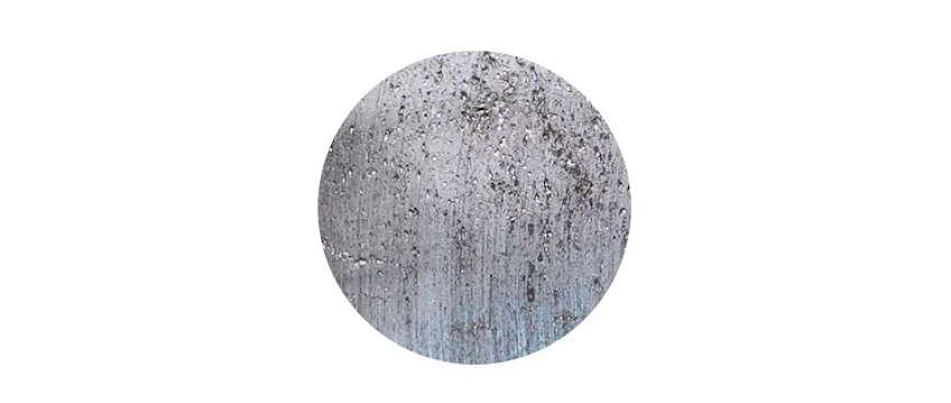
LA NORME NF EN ISO 12944-2 ET LA CLASSIFICATION DES ENVIRONNEMENTS CORROSIFS
Afin de déterminer et de classer les environnements corrosifs et la résistance des systèmes de peinture, il est nécessaire de se référer à la norme internationale, qui définit ces critères. La norme qui définit, évalue et limite ces paramètres est la norme NF EN ISO 12944-2, qui est axée sur des supports tels que :
- l’acier non protégé ;
- la galvanisation à chaud ;
- l’acier protégé par projection thermique de zinc.
Cette norme fait référence à différentes catégories d’environnement corrosif, divisées en 2 groupes :
- d’une part, il y a les catégories de corrosivité pour les environnements atmosphériques ;
- d’autre part, les catégories de corrosivité pour les structures immergées ou enterrées.
Catégories de corrosivité pour les environnements atmosphériques
Dans cette section, nous distinguons les catégories suivantes :
- Catégorie C1, pertes d’épaisseur de 1,3 micron pour l’acier. Cette catégorie est principalement destinée à l’évaluation des bâtiments chauffés dont l’atmosphère est propre, tels que les bureaux, les magasins, les écoles ou les hôtels.
- Catégorie C2, pertes d’épaisseur de 1,3 micron et jusqu’à 25 microns pour l’acier. Catégorie définie pour l’évaluation des atmosphères à faible niveau de pollution, ou des bâtiments non chauffés où la condensation peut se produire, par exemple les entrepôts, les centres sportifs, etc.
- Catégorie C3, pertes d’épaisseur de 25 microns et jusqu’à 50 microns pour l’acier. Cette catégorie est destinée à l’évaluation des atmosphères urbaines et industrielles, avec une pollution modérée au dioxyde de soufre, ou des usines avec une humidité élevée et une certaine pollution atmosphérique, par exemple les usines de transformation des aliments, les blanchisseries, les brasseries, les usines laitières.
- Catégorie C4, pertes d’épaisseur de 50 microns et jusqu’à 80 microns pour l’acier. Définie pour l’évaluation des zones industrielles et des zones côtières dont la salinité est modérée, telles que les usines chimiques, les piscines, les navires et les chantiers navals.
- Catégorie C5, pertes d’épaisseur de 80 microns et jusqu’à 200 microns pour l’acier. Analyse et évaluation des zones côtières et maritimes dont la salinité est élevée, ainsi que des bâtiments ou zones où la condensation est quasi permanente et la pollution est élevée.
- Catégorie CX, catégorie de corrosivité applicable aux environnements extrêmement corrosifs tels que les zones off-shore, les zones industrielles avec une humidité extrême, ainsi que les atmosphères agressives ou tropicales.
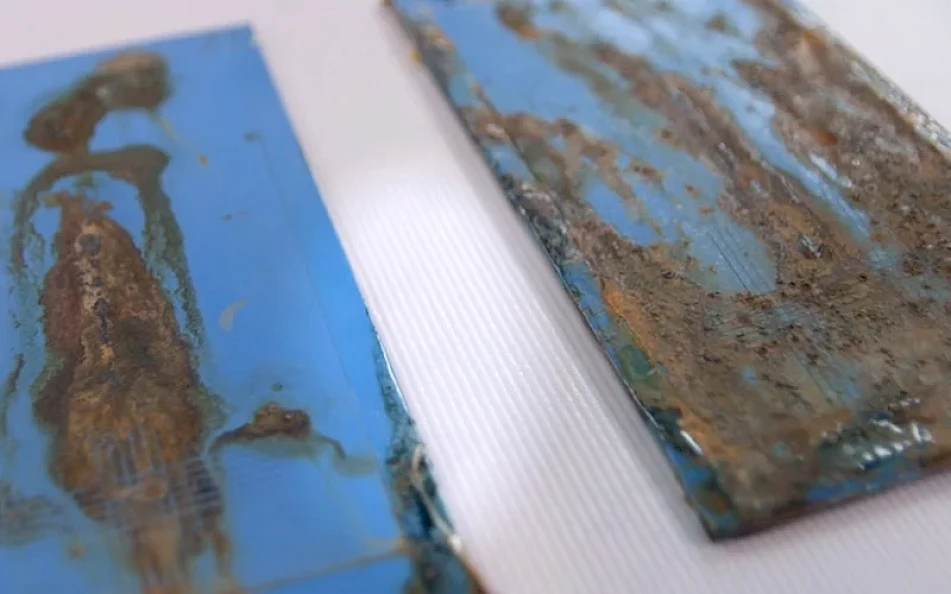
Catégories de corrosivité pour les structures immergées ou enterrées
- Catégorie IM1, pour les environnements d’eau douce tels que les installations fluviales et les centrales hydroélectriques.
- Catégorie IM2, pour les environnements d’eau de mer tels que les zones portuaires comprenant des structures comme les portes de confinement, les écluses, les docks et les structures offshore.
- Catégorie IM3, pour les structures enterrées telles que les réservoirs enterrés, les pieux en acier et les tuyaux en acier.
- Catégorie IM4, pour les structures situées en mer ou en eau saumâtre, telles que les structures immergées avec protection cathodique.
En outre, la norme NF EN ISO 12944-2 spécifie également la durabilité d’un système de peinture en fonction de trois intervalles de temps :
- Faible (L) : 2 à 5 ans
- Moyen (M) : 5 à 15 ans
- Élevé (H) : plus de 15 ans
SOLUTIONS POUR PRÉVENIR LA CORROSION EN PEINTURE
Peinture anticorrosion
Comme premier conseil, nous recommandons l’utilisation et l’application de produits anticorrosion haute résistance et durabilité, qui agissent comme une barrière efficace contre la corrosion.
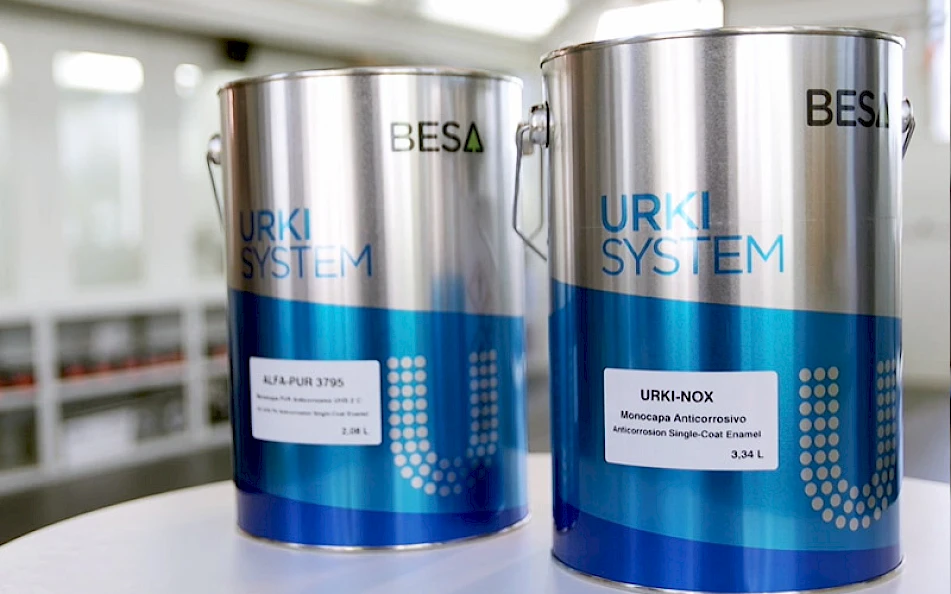
BESA dispose d’une large gamme de produits adaptés à une application sur différents types de supports, aux catégories de corrosivité et à différents secteurs, tels que les machines-outils, les structures métalliques, la chaudronnerie, les véhicules industriels et bien d’autres.
- Apprêts anticorrosion :
- Laques à accrochage direct 1C :
- Laques à accrochage direct 2C :
Systèmes de peinture anticorrosion – une protection durable et de qualité
D’un point de vue fonctionnel et économique, la corrosion est un problème qui a un impact direct sur le remplacement éventuel de pièces ou de machines, ainsi que sur leur entretien.
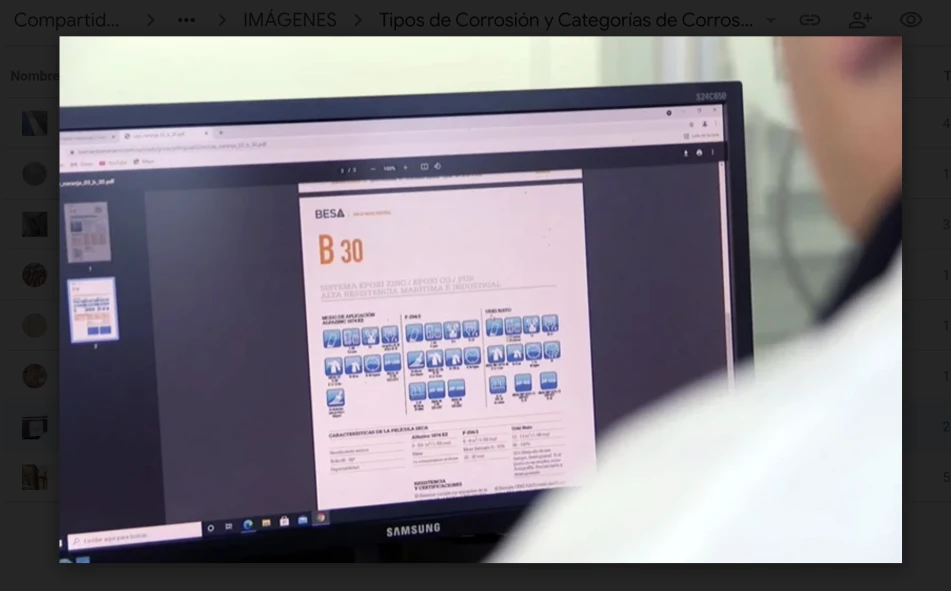
Le bon choix du système de peinture et de produits adéquats vous permettra d’espacer les périodes d’entretien et de réduire les coûts.
BESA dispose de différents systèmes de peinture conçus pour protéger efficacement tout type de surface métallique contre la corrosion, certifiés conformément à la norme NF EN ISO 12944. Ces systèmes peuvent varier en fonction des produits et des besoins de chaque application. Voici quelques systèmes :
Systèmes avec primaires 1C
- A-10. Système synthétique industriel de haute qualité
- Système destiné à la mise en peinture de structures métalliques, chaudronnerie, machines agricoles et travaux publics, ascenseurs, grues, matériel de construction, menuiserie métallique, carrosserie industrielle. Système conçu pour offrir une bonne résistance à l’oxydation et un travail de qualité à un coût moyen.
- Système certifié selon les exigences de la catégorie C3 (MOYEN) de la norme NF EN ISO 12944-2.
- A-25. Système mixte à haute résistance
- Système conçu pour la mise en peinture de structures métalliques, machines en général, travaux publics, carrosserie industrielle, etc. C’est un système à utiliser lorsqu’une grande résistance à l’oxydation et un travail de qualité sont requis. La laque présente une excellente dureté, élasticité, résistance à l’abrasion et aux agents agressifs.
- Système certifié selon les exigences de la catégorie C3 (MOYEN) de la norme NF EN ISO 12944-2.
Systèmes avec primaires 2C
- B-10. Système époxy Pur Industriel
- Système destiné à la mise en peinture de remorques et semi-remorques, citernes de camions, bétonnières, structures métalliques, etc. Le primaire F-294/2 offre la possibilité d’appliquer des finitions mouillé sur mouillé après 20-30 min. La laque Alfapur 3748 présente une élasticité, une consistance, une brillance et une résistance aux agents atmosphériques excellentes.
- Système certifié selon les exigences de la catégorie C3 (ÉLEVÉ) de la norme NF EN ISO 12944-2.
- B-15. Système époxy Pur Industriel, faible taux de COV
- Système destiné à la mise en peinture de remorques et semi-remorques, citernes de camions, bétonnières, structures métalliques, etc. Le primaire à teneur ultra-élevée en solides F-296/2, formulé avec des résines époxy et durci au polyamide, et haute teneur en pigments anticorrosion, confère au système de peinture une excellente protection anticorrosion.
- Système certifié selon les exigences de la catégorie C3 (ÉLEVÉ) de la norme NF EN ISO 12944-2.
- B-30. Système époxy Zinc-Époxy CG-Pur haute résistance milieu marin et industriel
- Système conçu pour la mise en peinture d’éléments du secteur électrique (transformateurs), éolien, grues portuaires et tout autre élément présentant des exigences de haute résistance.
- Système certifié selon les exigences de la catégorie C5 (ÉLEVÉ) de la norme NF EN ISO 12944-2.
Systèmes directs
- C-10. Système monocouche anticorrosion 1C
- Système conçu pour la mise en peinture dans des secteurs tels que les machines agricoles et les travaux publics, les véhicules industriels, les réservoirs, les tuyauteries, les structures métalliques, etc., (directement sur le support). Il a un aspect semi-brillant, il s’applique et s’étale facilement et offre un pouvoir de remplissage et un temps de séchage rapide.
- Système certifié selon les exigences de la catégorie C3 (FAIBLE) de la norme NF EN ISO 12944-2.
- C-20. Système monocouche anticorrosion UHS Pur 2C
- Système à teneur ultra-élevée en solides, conçu pour la mise en peinture de machines, silos, véhicules industriels, etc., avec des équipements fonctionnant en moyenne et haute pression. Il présente de l’élasticité et de la consistance, ainsi qu’une bonne résistance à l’oxydation sans besoin d’appliquer un primaire sur le support. Il est également utilisé comme alternative aux procédés conventionnels pour la réduction des émissions de COV dans les installations.
- Système certifié selon les exigences de la catégorie C3 (MOYEN) de la norme NF EN ISO 12944-2.